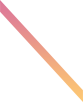
Case Study
Customer success stories – Find out how KAZE has moved these businesses smarter with our Automated Material Handling solutions
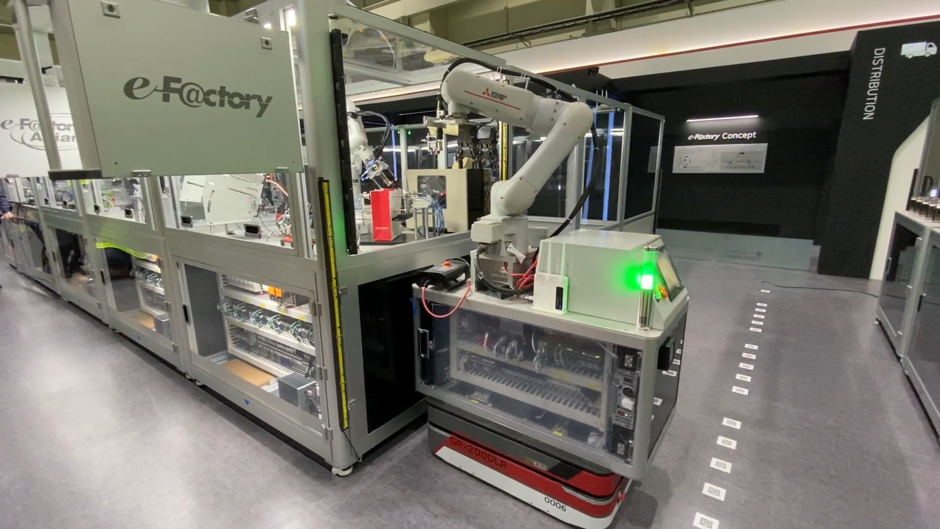
Mitsubishi South Korea, Manipulator for Automated Pick-and-Place
In pursuit of our goal of enabling robotics technology and moving materials smarter, Team KAZE successfully deployed our first Autonomous Mobile Robot in Mitsubishi South Korea. Working with Hyundai, the GR200 was retrofitted with a Mitsubishi Collaborative Robot (Cobot) Arm to pick-and-place the items between work stations at Mitsubishi’s factory shop floor. This is our first deployment beyond Southeast Asia, a significant milestone.
The standalone AMR deployed navigates via a defined grid and QR code. Mitsubishi is able to directly send commands to the AMR to move about from point to point and without a FMS. This allowed their skilled technicians to focus on their main role as they no longer need to man the system and transport the items manually. The nature of the application requires the accuracy, precision and yet flexiblity that QR code navigation provides. Built-in sensors allows the AMR to detect obstacles, reducing workplace injuries.
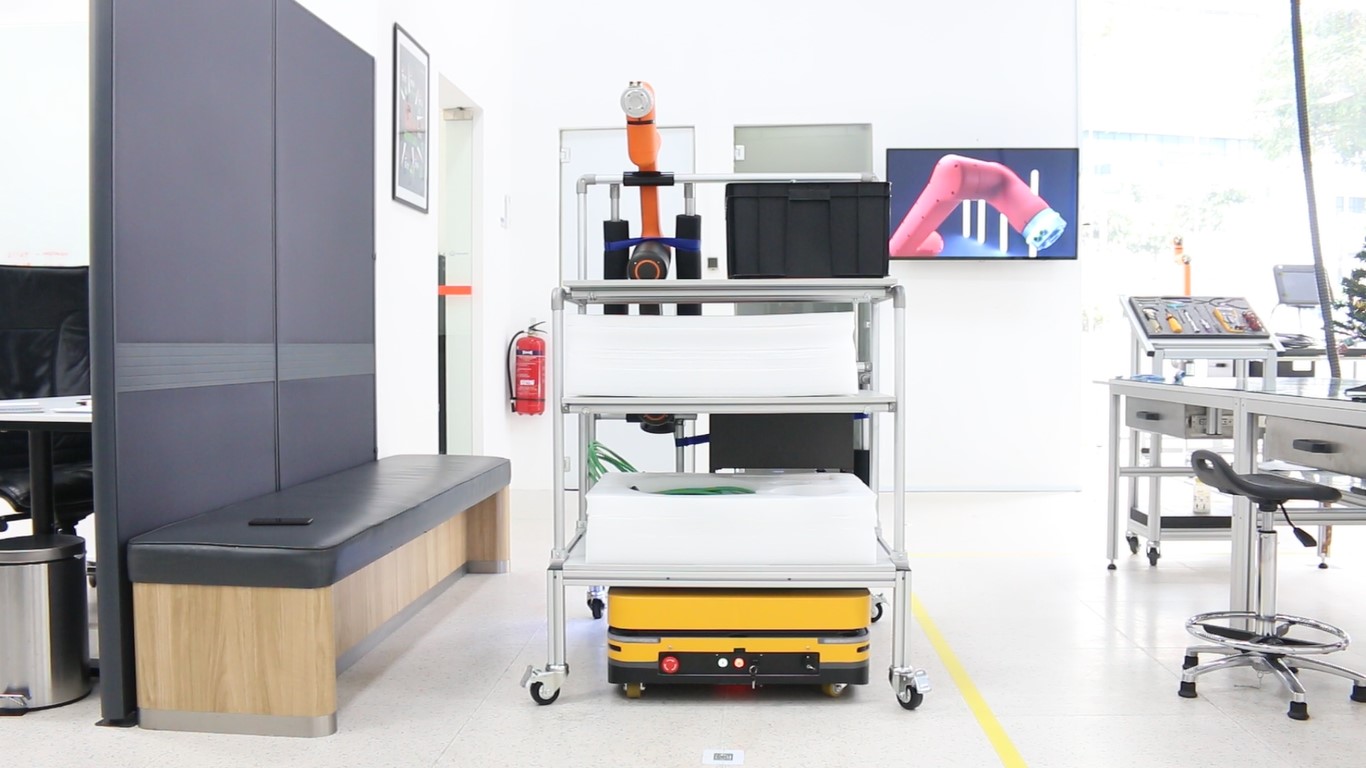
PBA-Hanwha, Automated transfer of materials for robotics assembly
KAZE delivered a scalable solution for the production clean room.
KAZE deployed GR-200DLR to transport assembly parts between production stages, driven by planning needs and software. This allowed their skilled technicians to focus on their main role as they no longer need to transport the items using trolley carts. The nature of their business required the flexible deployment our AMRs allow, which navigates using QR codes and enhanced with a vision camera to ensure accuracy. With built-in sensors to detect obstacles, workplace injuries are reduced.
The GR-FMS allocate jobs efficiently, eliminating both incorrect delivery location and damage during material handling, and provides management trackable data that can be used to identify bottlenecks and improve processes.
As a result of automation, they were able to increase operational hours by 33%, reduce labour costs by 40%, and increased employee satisfaction.